How to Prevent Refrigerant Leaks in Supermarket Systems?
- Share
- Issue Time
- Apr 12,2022
Summary
Reducing refrigerant leakage is very important and necessary. Reducing refrigerant leaks has five components: leak repair, leak detection, leak prevention, measurement/tracking performance, and goal setting. These five parts work together to address refrigerant leaks from all angles.
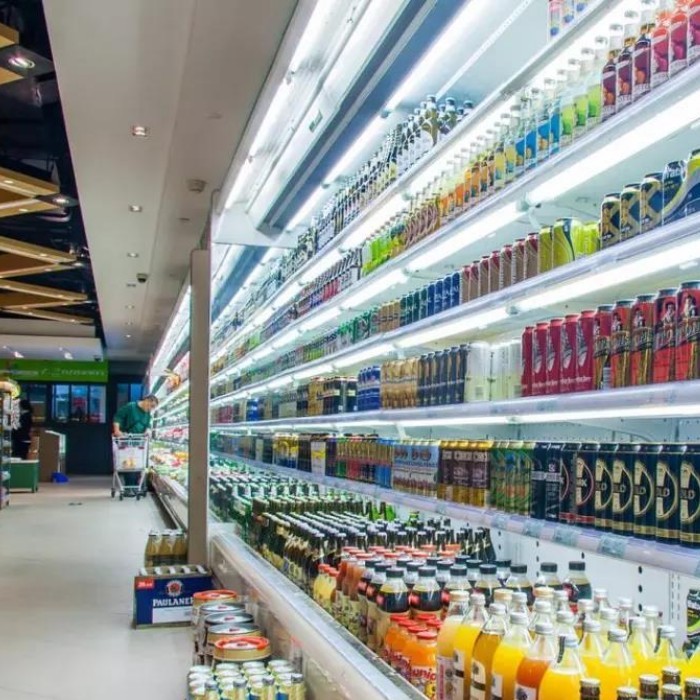
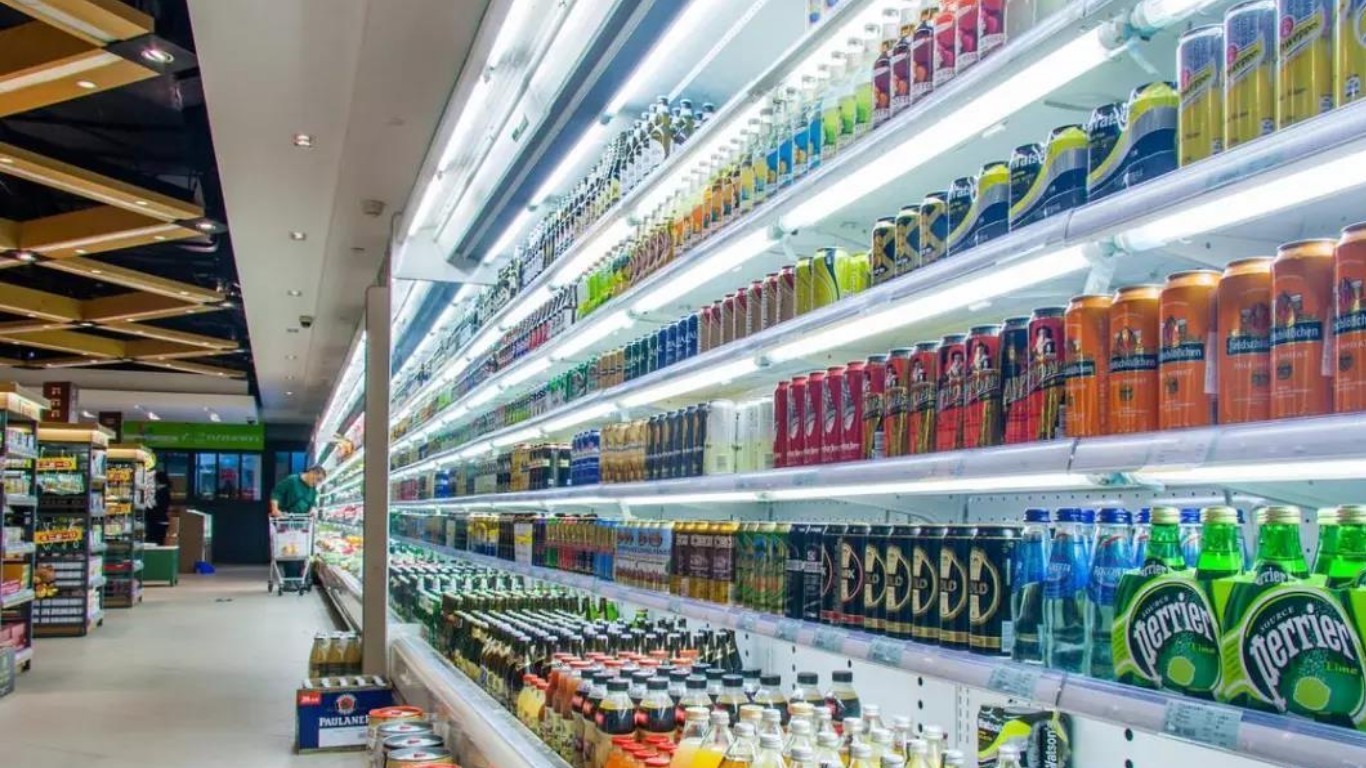
In the supermarket industry where profit margins are razor-thin, lowering costs is more profitable than increasing sales, and few cost items require improvement like a refrigerant leak.
Reducing refrigerant leaks can seem like a daunting task. Breaking this task down into manageable pieces reduces complexity and produces dramatic results quickly. A successful leak reduction program has at least five components: leak repair, leak detection, leak prevention, measurement/tracking performance, and goal setting. These five parts work together to address refrigerant leaks from all angles.
1) Leak repair
Those who want to reduce refrigerant leaks may find the first point too obvious: to reduce leaks, you must fix them.
The most used phrase in refrigerant management is "Of course, we fix all leaks". However, supermarkets in the country leaked about 1,000 pounds of refrigerant.
Most leaks will eventually be fixed, but when? How often do you wait to repair a leak until the store closes, until a repair technician can service you, or until the leak is so bad that your case can't keep its set temperature? Do you repair leaks only if the leak rate exceeds the leak repair threshold in the EPA refrigerant regulations? Did you shut down a device that couldn't be repaired right away? Unless your answer to these questions is never, never, never, never, you need to change your approach to leak repair if you want to make progress.
The elites in leak rates have figured this out. Every supermarket company I've come across with a leak rate of less than 10% has a "no spillage" policy. This means that you need to fix the vulnerability immediately.
2) Leak detection
Leak repair is followed by leak detection. When food overheats in a display case, do you first know you have a leak? If this is your leak detection method, you've leaked too much refrigerant. The faster a leak is detected the fewer refrigerant leaks.
There are a variety of leak detection options, ranging from sophisticated automatic leak detection systems to small hand-held leak detectors.
Stores with high leak rates may require monthly leak inspections for a period of time until the leak rate is brought under control. After that, quarterly inspections are usually sufficient for early detection. Yes, inspections cost money, but inspections can pay for themselves by reducing refrigerant costs.
Supermarket companies with extremely low leak rates stipulate that each leak repair activity ends with a "walk-through" of the store using a leak detector before the repair technician leaves the store. Before completing the follow-up leak repair verification tests required by EPA Section 608 regulations, technicians can often complete the drill while the technician waits for the repaired equipment to return to normal operating condition.
3) Leak prevention
Most companies will see a significant increase in their leak rates with no leak tolerance policies and systematic leak detection methods. But if that's where your plans stop, you're missing out on the most important way to reduce environmentally harmful and expensive refrigerant leaks: refrigeration technology designed with leak prevention in mind.
For example, secondary systems use less refrigerant, so fewer refrigerant leaks, and the smaller refrigerant charge is limited to the machine room, allowing leaks to be detected and repaired faster. In addition to being typically characterized by low leak rates, secondary systems also maintain low leak rates for extended periods of time after installation. Circulating piping, reducing the number of piping connections, and valve covers are other examples of preventing leaks in equipment.
4) Measurement/tracking performance
The next two parts of any appreciable leak reduction program are less obvious than leak repair, leak detection, and leak prevention. Few food retail companies set annual refrigerant-related goals and measure performance; however, these same companies measure and set goals in most other areas of their business. They stick to the old adage that you can't improve what you can't measure. So why don't you deal with refrigerant leaks the same way?
There are many cooling-related performance factors you can measure, but the following four are the basics.
Company-wide annual leak rate
What was the leak rate for all refrigeration and air conditioning equipment in all your stores during the calendar year? If you don't know the number, and a lot of people don't, you have to figure it out. This metric includes the amount of refrigerant in all refrigeration and air-conditioning equipment divided by the amount of refrigerant leaking from that equipment in the calendar year.
Since every supermarket across the country has laws that require keeping track of how much refrigerant is in each store's refrigeration and air conditioning equipment, and how much refrigerant is leaking from that equipment, it shouldn't be difficult to get these things in place.
Pounds of refrigerant leaked
However, the leak rate is not the whole story, as blindly sticking to the leak rate as a metric can lead to errors. Seeing the pounds of refrigerant leaking at each store can help you prioritize investments in spill reduction activities. For example, you might have two stores with a 70% leak rate, but one store leaked 3,000 pounds of refrigerant and the other 300 pounds of refrigerant. Of course, you want to prioritize stores that leak 3,000 pounds of refrigerant.
Leak repair response time
Leak repair response time is a measure of how quickly technicians respond to leak repair requests. If you have an automatic leak detection system, you will measure the time between an alert and a service technician's response. You can define "response" in your own way;
For example, when a technician arrives at a store, triages a leak over the phone, or when a contractor deploys a technician to the store. This is in minutes. As far as I know, there is no supermarket industry average for this number and no rule of thumb on what you should measure. Some companies categorize alerts into categories such as the size of the leak (i.e. catastrophic leak, small leak, etc.) or the location of the leak (i.e. compressor, display case, etc.). Then they measured the response time for each category. Others just measure the average time per year and try to improve it.
Time to fix leaks
The average time to repair a leak is measured as is the leak repair response time. Be prepared to have your service contractor argue that this measure is unfair, as different types of leaks take more or less time to fix. The key is to look at the annual average for the entire company, which may include multiple contractors. This way, you can measure the success of your existing process, rather than the time to fix individual incidents that may not be comparable.
5) Set goals
After measuring whatever you think you need to measure, the next step is to set improvement goals. First, ask yourself what you want to achieve. You may feel that continuous improvement is the priority, not actual numbers. If this is the case, a 10% annual increase in leak rate and lbs of refrigerant leaked is considered achievable. Of course, it depends on your starting point. If your company-wide annual leak rate is 50%, you should be able to reduce it by 20-25% within a year. If your starting leak rate is below 12%, a 10% reduction is probably the most you want.
If your goal is a realistic number, such as a company-wide target of a 15% annual leak rate, which is a respectable average leak rate, you need to determine how long it will take to achieve that number, and then determine the level of improvement required each year in order to finally achieve your desired goal.
Reducing refrigerant leaks, like other aspects of good business management, can lead to a better bottom line. If you want to purchase compliant refrigerant for your store or company to reduce the chance of refrigerant leakage, please contact us.
Fotech is a professional refrigerant supplier and manufacturer with more than 15 years of experience in the distribution of environmentally friendly refrigerants, cleaning agents, fire extinguishing agents, foaming agents, cleaning agents, and new high-performance chemical materials. We support and comply with regulations to help you select suitable alternatives with less environmental impact, while still providing effective cooling and cooling capacity.